How a Robot Welder Can Futureproof Your Fabrication Business
The manufacturing world is changing – fast. With rising labour costs, tighter deadlines, and increasing pressure for consistency, staying competitive means embracing smart technology. That’s where the robot welder comes into play.
Once only seen in high-budget automotive plants, robotic welding systems are now accessible to businesses of all sizes. And for many fabricators, they’re becoming a vital piece of the puzzle. What was once a futuristic idea is now a practical and necessary step for staying ahead in a competitive market.
What Makes a Robot Welder Different?
Unlike a manual welder who needs breaks and supervision, a robot welder is built to run continuously, day and night. It doesn’t fatigue, doesn’t vary in quality, and doesn’t require constant oversight. Once programmed, it can weld identical parts with incredible accuracy – every single time.
These robotic systems are ideal for high-volume or repetitive tasks, where even a minor variation could lead to quality issues or rework. They also improve safety by reducing human exposure to fumes, heat, and dangerous workspaces.
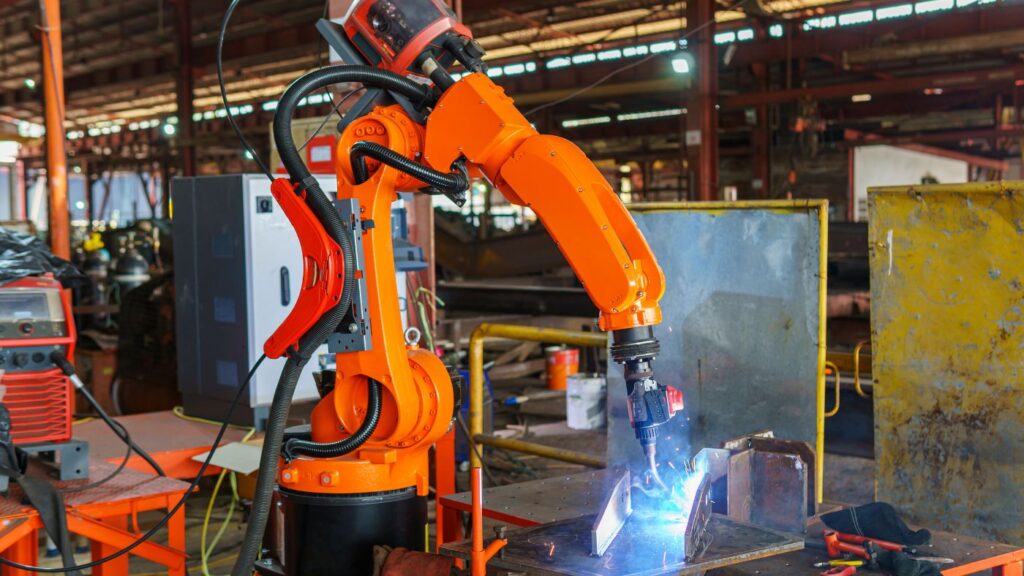
Source: vissteel.com.vn
The Pressure to Deliver Is Growing
Customer expectations are higher than ever. Whether you’re building custom frameworks, structural components, or precision parts, clients want faster delivery, lower costs, and top-quality finishes. That’s a hard balance to strike without automation.
By adding a robot welder to your production line, you’re not just speeding up the process – you’re removing the risk of inconsistency, freeing up skilled workers, and unlocking new capacity without needing to expand your team. Your workforce can shift focus to more complex and value-driven tasks.
A Long-Term Investment in Growth
Admittedly, a robot welder isn’t a minor expense. But when you factor in the savings from reduced labour costs, fewer errors, and faster turnaround times, the numbers often speak for themselves.
And it’s not just about efficiency. Automation also makes your business more scalable. Taking on larger contracts, shorter lead times, or multi-shift work becomes far more feasible when you’ve got a machine that doesn’t sleep. In a world where agility is crucial, this adaptability is priceless.
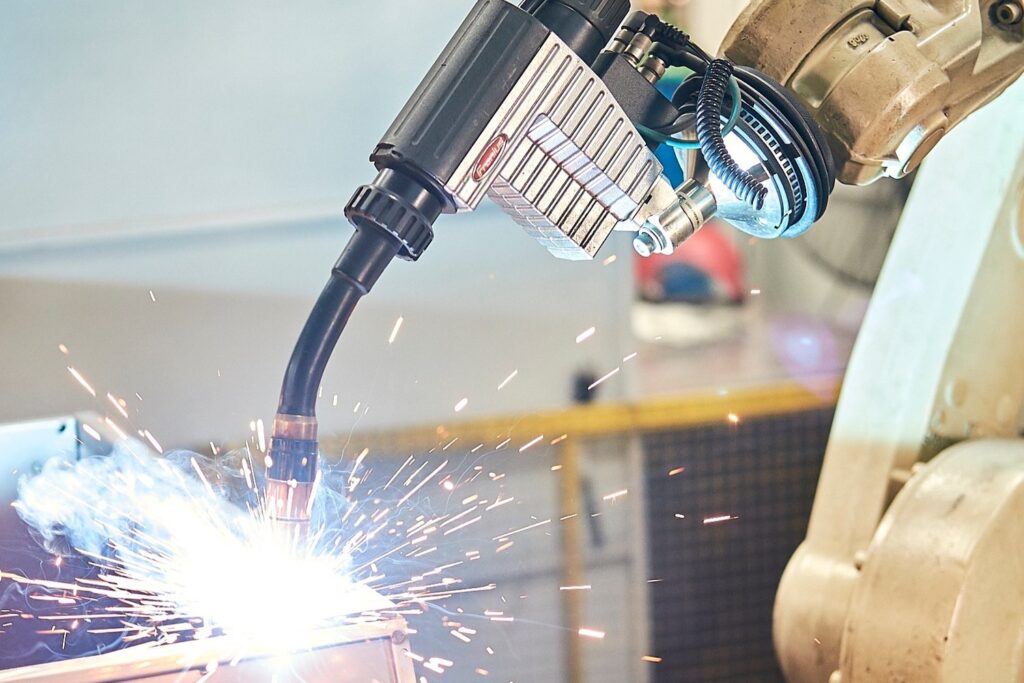
Source: idealdesign.com
What Industries Are Already Using Robot Welders?
- Automotive ─ From chassis to exhaust systems, cars rely heavily on precision welds.
- Agriculture ─ Farming equipment manufacturers use robots for structural components and brackets.
- Construction ─ Beams, frames, gates, and railings – all benefit from robotic welding.
- Furniture & fixtures ─ Welded metal furniture, shelving, and display units can be mass-produced with ease.
Even small fabrication shops are beginning to explore compact robotic systems that suit lower-volume, high-precision work.
Final Word
If you’re still relying solely on manual welding, you might be missing out on a major competitive advantage. A robot welder isn’t just a machine – it’s a gateway to greater efficiency, consistency, and growth.
Whether you’re scaling up or simply looking to streamline your operation, robotic welding could be the smartest move you make this decade. Now is the time to rethink how your business can work smarter – not just harder.
