How Do You Make A Bad Weld Look Good
If you are planning to buy your first welding machine, you need to be well acquainted with this tool. Welding machines are very useful but only when they are handled properly. Otherwise, you can get the exact opposite effect. What then can we do and how can we make a bad weld look good, or at least better? We will give you some answers.
Welding And How to Do It
Welding is the procedure of joining the same or different materials, by melting or pressing. It is done with a welding machine, with or without using some additional material – in such a way as to obtain a homogeneous mixture that will be welded. Of course, the technology of work depends on the type of welding and the machine you use.
In this regard, we distinguish several types of welding machines, and these are devices for electric arc, gas, and spot welding. If we talk about amperage, in recent years, so-called inverter welding machines are increasingly used – which more efficiently convert input current to welding current at high frequency. Due to inverter technology, welding machines are becoming smaller and lighter, gaining in portability.
Making A Bad Welding Look Better
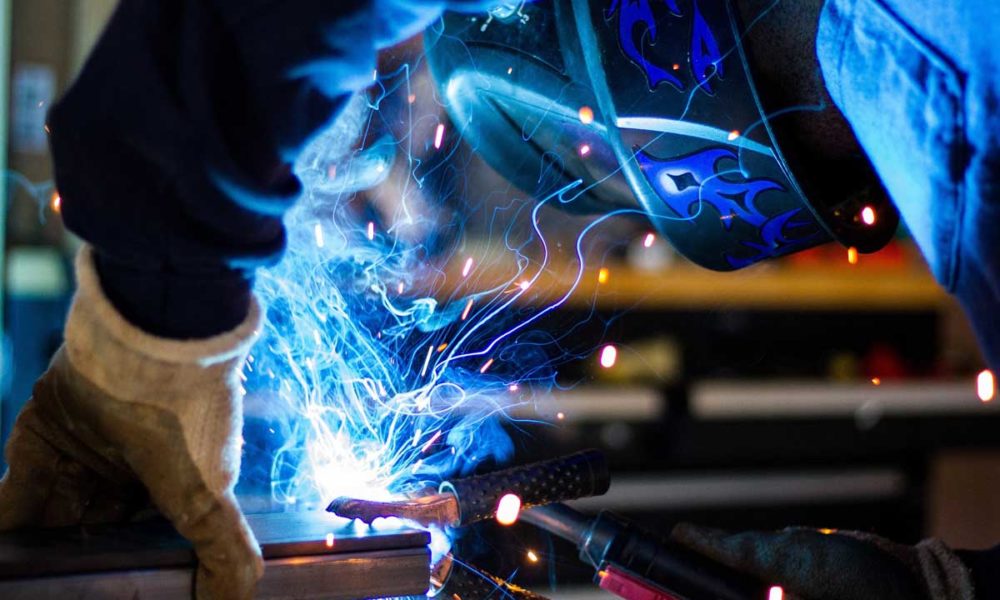
Source: highwaysystemsinc.com
Whichever welding machine you use, mistakes are possible, and even certain if you are a beginner. So how then to correct mistakes and make bad welding look good?
Cracks in the welded spot
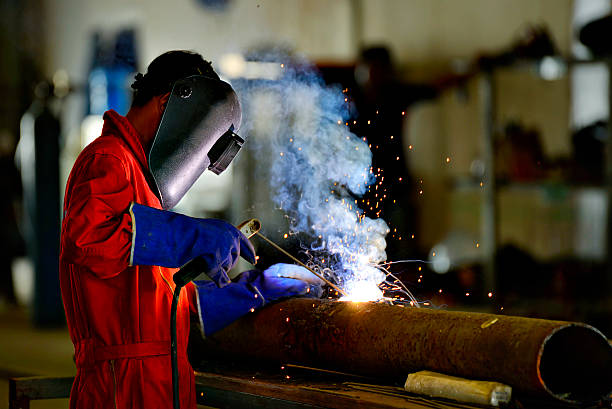
Source: istockphoto.com
It happens that cracks are formed during welding. Not only does it not look aesthetically pleasing – but it can also be very inconvenient because the cracks spread and become wider over time. Want to fix this and make it look better? If the cracks have appeared, they should first be sanded, cleaned, leveled – and then a new weld should be made. Just be sure you do it at a slightly higher temperature, to make the joint better.
Deformed weld
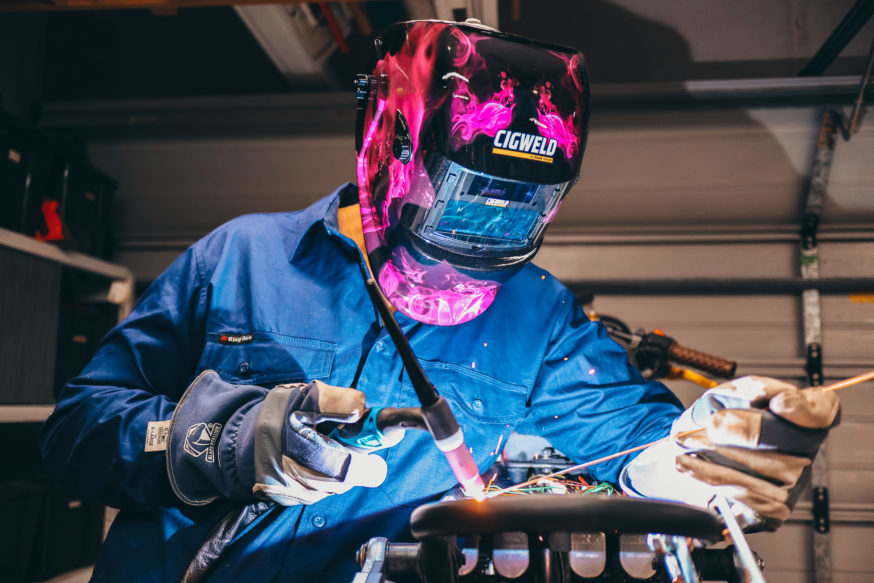
Source: cigweld.com.au
High temperatures are used in metal welding. After that, we have to wait for the welded place to cool and harden. It is then that deformations occur during the cooling and hardening of the metal joint. This happens most often due to poor placement of metal joints or insufficient tightening. Better fixing of the parts to be joined, as well as welding on both sides of the joint – can prevent these situations or fix the defect to some extent if it occurs.
Permeability and brittleness
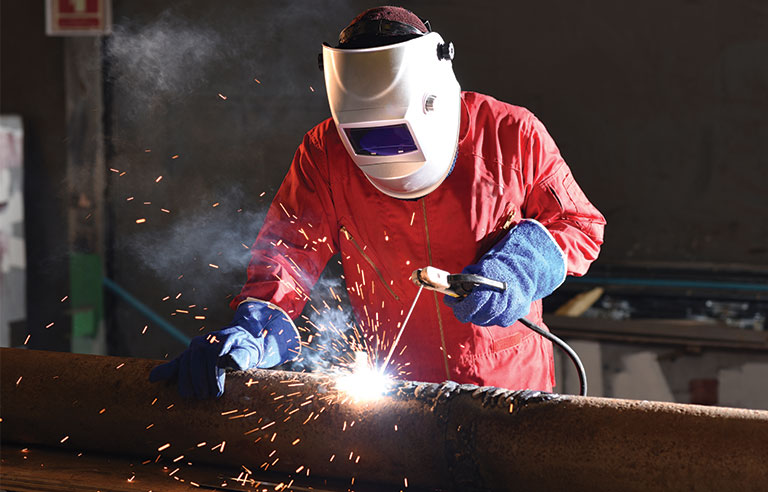
Source: safetyandhealthmagazine.com
Such defects most often happen due to the leakage of substances such as hydrogen, oxygen, or nitrogen during the melting procedure. When this type of permeability occurs, there are additional problems such as corrosion, moisture leakage, grease, or dirt on the weld. These are the factors that influence the spot you are welding in a way it starts to further weaken, becomes brittle, and eventually, crack.
If you want to fix this situation, it is recommendable to repeat the entire procedure. However, it is advisable to use new welding material and see whether the burner on the device needs to be checked out. If necessary, clean the nozzle on the burner and perform the whole procedure again using fresh material.
The Bottom Line
Problems like these happen not only to beginners but also to professional welders. Therefore, it should be borne in mind that it is very important to choose a good welding machine. Certainly following your needs, but also with the training to handle these devices properly.
